Top 5 Field Service Capabilities To Boost Manufacturing Operations (Winter ‘24)
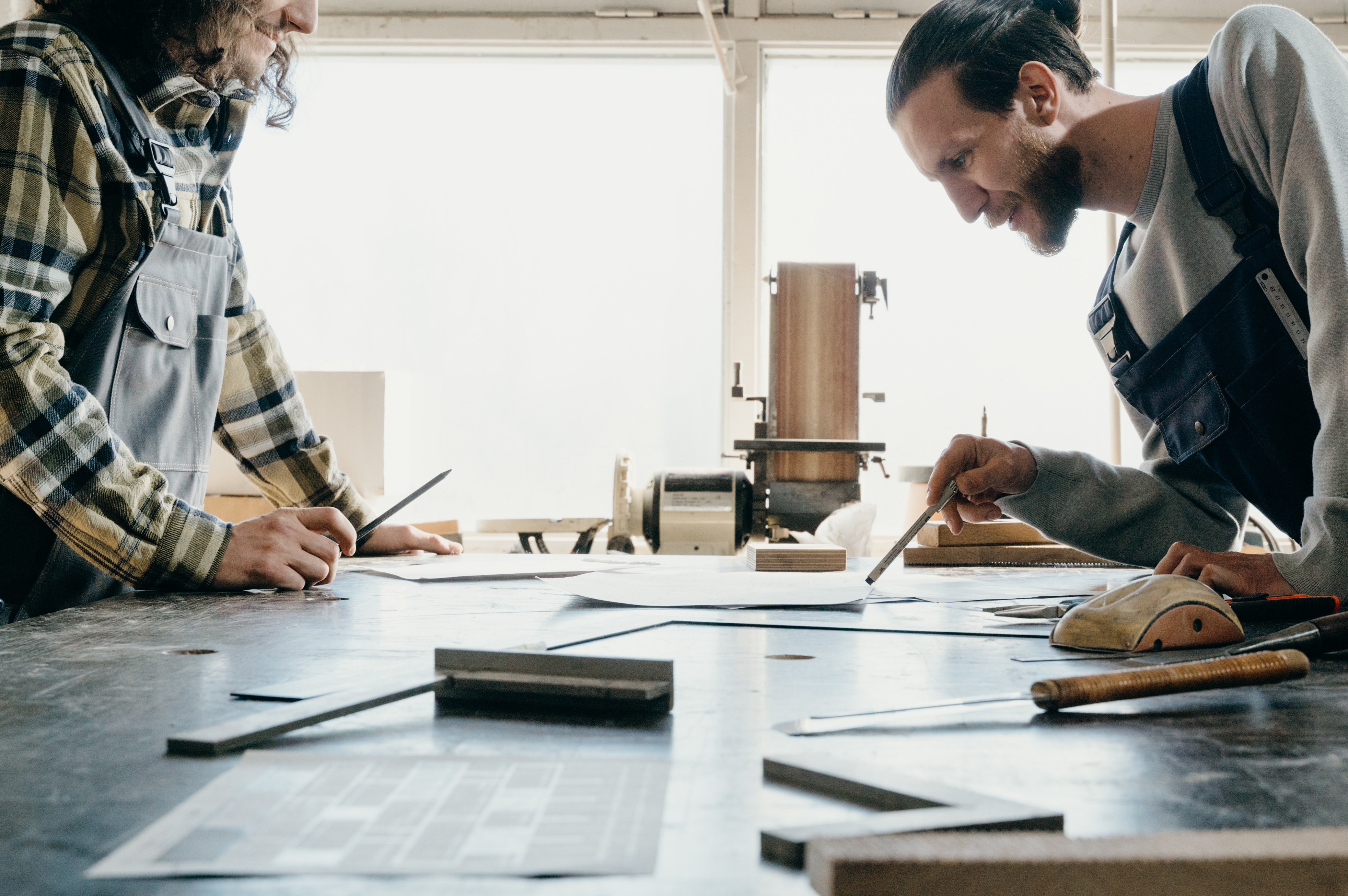
Salesforce Field Service is releasing some great new enhancements in their Winter ‘24 release that can really improve efficiency for manufacturing field teams. As someone who has worked with manufacturers for most of my career, I wanted to share 5 upgrades that caught my eye:
- Optimized Scheduling for Complex Jobs
As we know, large equipment installs and maintenance projects often span multiple sites and days. This can get messy fast when trying to schedule tightly with the right techs and parts in each location. The new scheduling engine helps optimize the full project while considering technicians skills, workload and availability. This prevents the kinds of delays that drive customers crazy.
- Barcode & NFC Scanning in Custom Apps
While barcode scanning has always been a feature of Field Service, the ability to bring this into our purpose built screens has not. We can now use NFC tap or scan equipment serial numbers and part codes directly which saves a ton of time. No more squinting to manually type in those long serial numbers or risking incorrect part data!
- Automated Location-Based Time Tracking
It used to be a pain remembering to manually clock in and out at each site. With the new location tracking features, the mobile app automatically records when technicians arrive on-site based on GPS. No more forgetting to clock in and out or entering incorrect times!
- Branded Field Reporting From Mobile
One of my favorite releases from this winter, the new Document Builder helps technicians quickly generate polished, branded field reports right from the app. Technicians can include photos, signatures, custom fonts - the works! This makes our brand image shine and gives customers nice documentation of all work completed.
- Real-Time Asset Health Monitoring
Finally, the new asset dashboards provide instant alerts if any sensor readings from the field are out of spec. We can catch problems proactively before equipment fails. No more 2am call outs to fix overly-hot bearings!
These upgrades solve real headaches faced daily as field technicians. I'm especially excited about the scheduling, custom barcode scanning features, automated time tracking, and real-time asset health alerts. What do you think? Which capabilities seem most useful for our team.
We’d love to hear your thoughts! Contact us today.